Forklifts play a crucial role in various industries, facilitating the movement and lifting of heavy loads with ease and a massive amount of customisability. Whether you’re a warehouse manager, logistics professional, or a newcomer to the material handling world, understanding the basics of forklifts and forklift maintenance is essential.
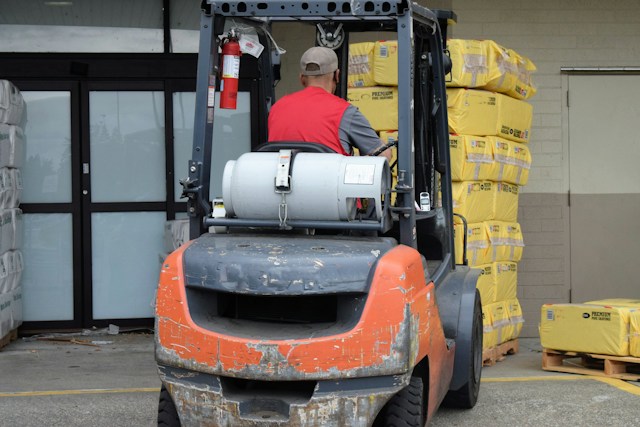
Starting and Operating Your Forklift:
Pre-Operational Checks:
Before starting your forklift, it’s essential to perform a series of pre-operational checks. Inspect the tires for proper inflation, check the oil and fluid levels, ensure the brakes are functioning correctly, and examine the forks for any signs of damage. This routine check ensures that the forklift is in good working condition and reduces the risk of accidents.
Starting the Forklift:
Familiarise yourself with the forklift’s controls and start the engine according to the manufacturer’s instructions. Most forklifts have a key-operated ignition, while others may use a push-button start. Ensure that the seatbelt is securely fastened before moving the forklift.
Basic Operation:
Understanding the forklift’s controls is crucial for safe operation. The accelerator, brake, steering, and lifting controls should be operated smoothly and with precision. Take the time to practise basic manoeuvres, such as forward and reverse driving, turning, and lifting and lowering loads, in a controlled environment.
Load Handling:
Proper load handling is a critical aspect of forklift operation. Assess the weight and stability of the load before attempting to lift it. Ensure the load is evenly distributed on the forks, and use the appropriate lifting attachment if needed. Avoid overloading the forklift, as this can compromise stability and pose safety risks.
The Importance of Forklift Maintenance:
Enhanced Safety:
Regular maintenance is not just about ensuring the forklift’s longevity; it is also a key factor in promoting safety in the workplace. Well-maintained forklifts are less likely to experience malfunctions or breakdowns during operation, reducing the risk of accidents and injuries.
Optimal Performance:
A properly maintained forklift operates at peak performance. Regular servicing helps identify and address issues before they escalate, ensuring that the forklift can handle its intended workload efficiently. This, in turn, contributes to increased productivity in the workplace.
Compliance with Regulations:
Most countries and regions have strict regulations regarding forklift maintenance. In New Zealand, some forklifts require a Warrant of Fitness (WOF). Adhering to these regulations not only ensures a safe working environment but also helps companies avoid penalties and legal consequences associated with non-compliance.
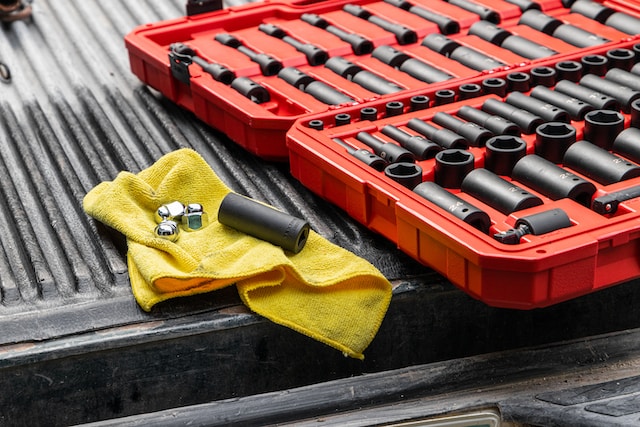
Forklift Maintenance Checklist:
Maintaining a forklift is a comprehensive process that involves regular inspections, scheduled servicing, and addressing specific components prone to wear and tear. Here’s an in-depth look at the maintenance checklist and why each aspect is crucial:
Daily Inspections:
- Fluid Levels: Regularly check and maintain appropriate levels of engine oil, hydraulic fluid, coolant, and brake fluid. Low fluid levels can lead to system failures, reduced efficiency, and, in extreme cases, irreversible damage to critical components.
- Tire Condition: Inspect tires for wear, cuts, and punctures daily. Worn-out or damaged tires can affect stability, load handling, and overall safety. Replace tires promptly to avoid accidents and ensure optimal performance.
Scheduled Servicing:
- Periodic Fluid Changes: Over time, engine oil, hydraulic fluid, and coolant can become contaminated, leading to decreased lubrication and increased friction. Regularly changing fluids per the manufacturer’s recommendations ensures the smooth operation of the forklift’s various systems.
- Component Inspections: Scheduled servicing involves in-depth inspections of components such as the transmission, brakes, steering, and hydraulic systems. Identifying and addressing potential issues early on prevents major breakdowns and ensures the forklift’s reliability.
Battery Maintenance:
- Charging Procedures: Follow proper battery charging procedures to maintain its efficiency and lifespan. Overcharging or undercharging can lead to premature battery failure, reducing the forklift’s operational time and productivity.
- Watering and Cleaning: Regularly check and maintain the water levels in lead-acid batteries. Clean the battery terminals and connections to prevent corrosion. Proper battery maintenance is crucial for electric forklifts to operate efficiently.
Replacement Parts:
- Tires: Forklift tires are subject to considerable stress, especially in industrial environments. Worn-out or damaged tires compromise traction, stability, and load-handling capabilities. Replacing tires at the right time ensures optimal performance and reduces the risk of accidents.
- Brake Components: Forklift brakes undergo significant wear due to frequent stops and starts. Worn brake pads or damaged brake components can lead to decreased stopping power and compromised safety. Regularly inspect and replace brake components as needed.
- Filters: Air, fuel, and hydraulic filters play a crucial role in maintaining the forklift’s performance. Dirty or clogged filters can lead to decreased engine efficiency and increased fuel consumption. Replace filters at regular intervals to ensure optimal engine function.
- Hydraulic Components: Hydraulic systems are integral to forklift operation, and components such as hoses, seals, and pumps are prone to wear. Leaks or malfunctions in the hydraulic system can result in decreased lifting capacity and operational inefficiencies. Timely replacement of worn hydraulic components is essential.
Training and Documentation:
- Operator Training: Well-trained operators contribute significantly to forklift longevity. They should be educated on proper operation, routine inspections, and prompt reporting of any issues. This proactive approach helps prevent potential problems.
- Detailed Records: Maintaining detailed records of all maintenance activities is not only a regulatory requirement but also a valuable tool for tracking the forklift’s history. These records aid in identifying patterns of wear, predicting potential issues, and ensuring compliance with manufacturer guidelines and industry regulations.
A meticulous forklift maintenance checklist, including daily inspections, scheduled servicing, and timely replacement of worn parts, is essential for ensuring the safety, reliability, and optimal performance of your forklift. By adopting a proactive approach to maintenance, businesses can minimise downtime, extend the lifespan of their equipment, and create a safer working environment for their operators.
Conclusion
In conclusion, a solid understanding of forklift operation and maintenance is essential for both newcomers and seasoned professionals in the material handling industry.
By incorporating regular pre-operational checks, adhering to proper maintenance schedules, and addressing issues promptly, you can ensure the longevity, safety, and optimal performance of your forklift.
Remember that a well-maintained forklift is not only a reliable tool for material handling but also a key contributor to a safe and efficient workplace. Make sure to get in touch with your local forklift specialists if you have any concerns or further questions,